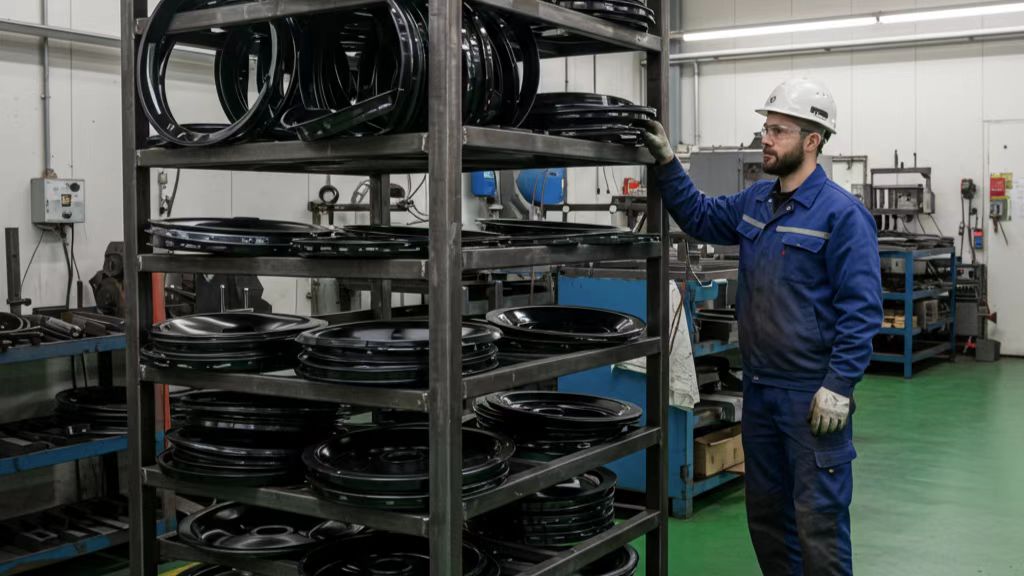
After plastic injection molding, surface problems are a common challenge. These issues not only affect the appearance of the product, but can also degrade performance. Aftertreatment technology provides a solution for this. Effectively solve the surface problems of plastic injection products. From traditional grinding and polishing, to modern spraying electroplating, to the emerging laser plasma treatment, each has its own characteristics. Next, we will go into detail about these technologies and their applications when solving different surface problems.
What are the problems with the molded surface?
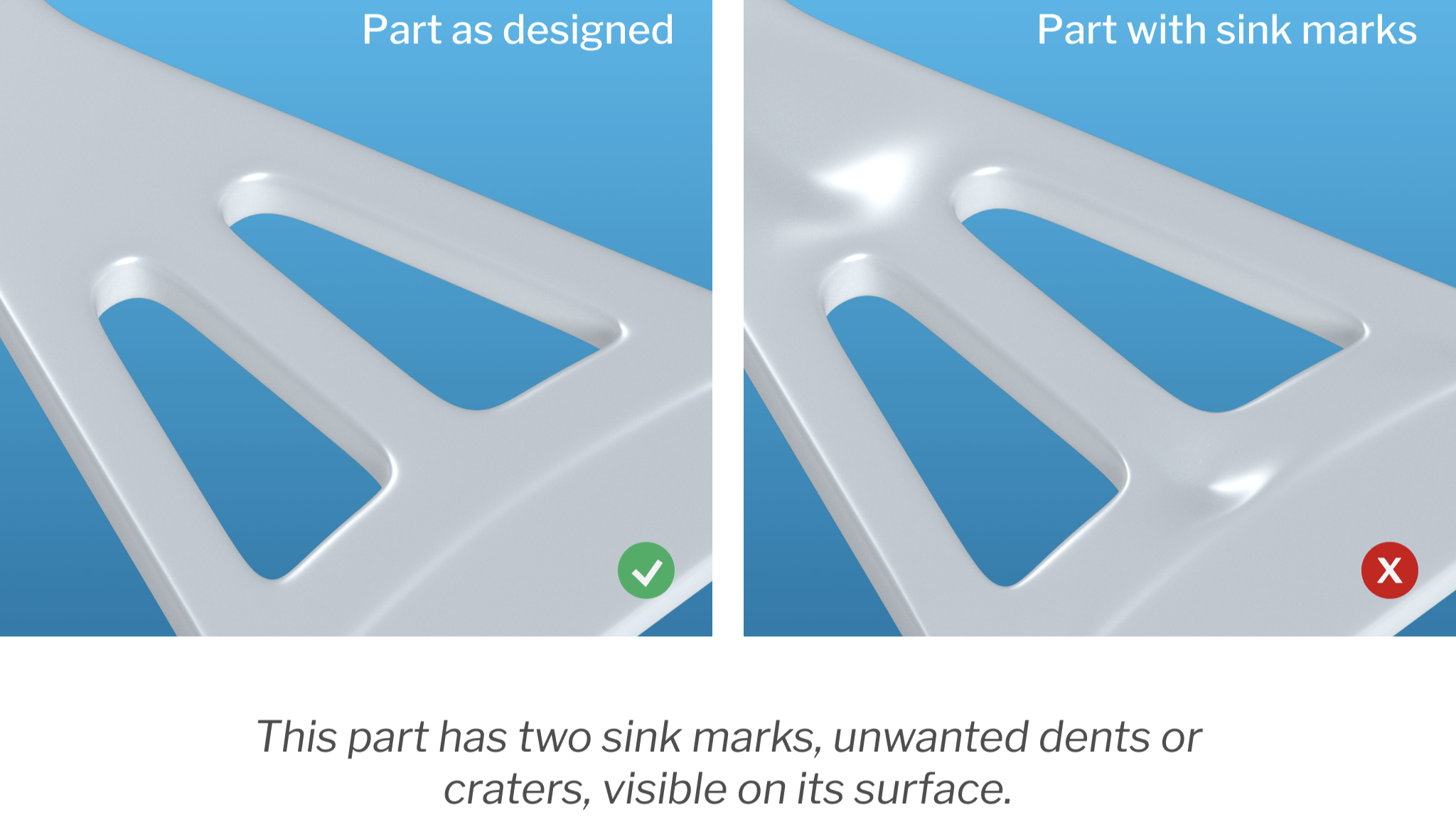
In the process of plastic injection molding, various problems may occur on the surface of the finished product due to the influence of a variety of factors. These issues can affect the appearance, performance, and longevity of a product.
- Sink marks: Sink marks are surface depressions caused by uneven cooling and shrinkage of plastics.
- Weld line: Weld line is a surface trace formed by insufficient bond of plastic melt.
- Air bubbles: Air bubbles are surface or internal cavities formed by gas trapped in plastics.
- Scratches: Scratches are linear marks produced by mechanical damage to the surface of a product.
- Uneven gloss: Uneven gloss is a phenomenon of uneven gloss distribution on the surface of the product.
- Ripple: Ripple is a wavy pattern on the surface caused by the flow of melt in the mold, which is hindered by mutual extrusion and alternation.
- Jet Pattern: Jet pattern is a surface defect caused by the melt not fully forming a flow crest in the mold cavity.
- White mist: White mist is a surface phenomenon caused by the failure of the gas inside the melt to enter the mold cavity.
What post-treatments can improve the injection surface?
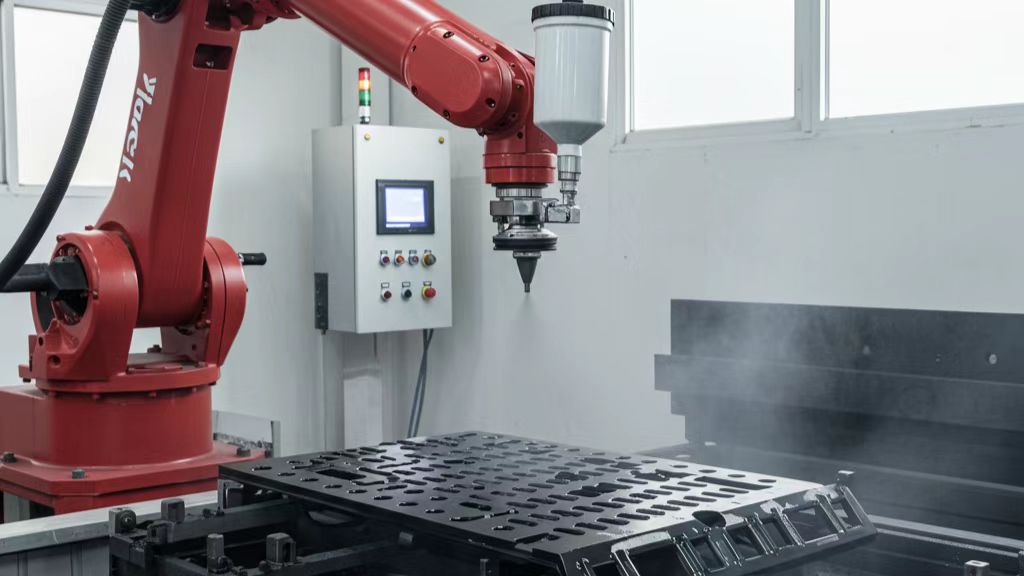
After plastic injection molding, a variety of post-treatment techniques can be employed to improve the surface quality. The following post-processing technologies can provide solutions to different surface problems, thereby improving the quality and appearance of molded products.
- Grinding and polishing: Mechanical removal of surface defects, such as scratches and roughness, to make the surface smoother.
- Spraying and coating: Spraying a layer of paint on a plastic surface can improve appearance, abrasion and weather resistance.
- Electroplating: Deposition a layer of metal on the surface of the plastic can improve the conductivity, wear resistance and appearance texture of the product.
- Laser Treatment: Precise removal or modification of surface materials using a laser beam enables fine surface treatment and pattern etching.
- Plasma treatment: Plasma is used to change surface properties to improve the adhesion, cleanliness and surface energy of materials.
- Chemical treatment: treatment of plastic surfaces by chemical reagents, such as chemical polishing, chemical etching, etching, etc.
How to choose the right post-processing?
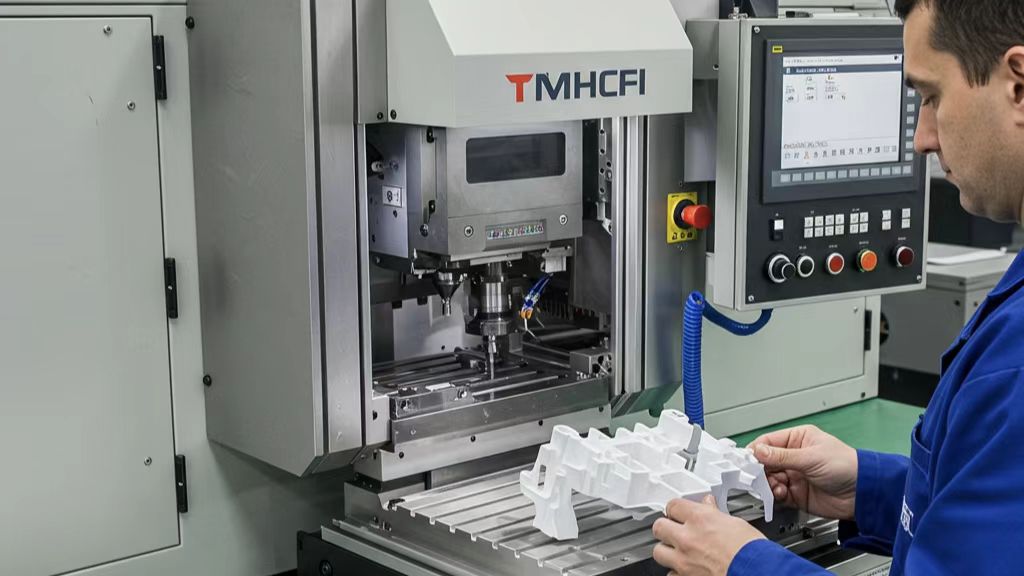
Choosing the right post-processing method requires a combination of factors such as product material, type of surface problem, product shape and size, performance requirements, cost factors, production efficiency and environmental requirements.
- Product material: Select a compatible post-processing technology according to the characteristics of the plastic material.
- Surface Problem Type: Select a post-treatment method that can be effectively improved for specific surface defects.
- Product shape and size: Consider the complexity and size of the product to select the appropriate post-processing process.
- Performance requirements: According to the use needs of the product, choose the post-processing solution that can provide the required performance.
- Cost factor: on the premise of meeting the quality requirements, choose an economical and reasonable post-processing scheme.
- Production efficiency: Choose a post-processing method that can meet the production rhythm and output.
- Environmental protection requirements: choose green and environmentally friendly post-treatment technology with less impact on the environment.
Summary of plastic injection surface problems and their causes
Cosmetic issues |
genesis |
Detailed description and impact |
harm |
Sink marks | The material has uneven cooling and shrinkage, uneven wall thickness, and insufficient holding pressure | The surface is concave, affecting appearance and strength, especially in thick walls. | Reducing the structural strength of the product affects the dimensional accuracy of the product, which may lead to early failure of the product. |
Scratches | Demoulding damage, transportation friction, and rough mold surface | Linear damage to the surface, which affects the appearance and may reduce the wear resistance of the surface. | Affect the appearance of the product, reduce the surface protection ability of the product, and may lead to premature wear of the product. |
corrugation | The melt flow is blocked, the mold design is not reasonable, and the injection speed is unstable | The surface is wavy, which affects the appearance and may affect the accuracy of the product. | Affects the surface flatness of the product and may lead to product assembly problems. |
crack | The injection pressure is too high, the mold temperature is too low, and the strength of the material itself is insufficient | Cracks appear on the surface or inside, which affects the strength of the product and is easy to break under stress. | The product structure is damaged, resulting in the direct scrapping of the product. |
Injection surface defects and prevention
Plastic injection surface defects affect the appearance and performance of products, the selection of dry and clean materials, optimization of mold design, control of process parameters, is the key to prevent defects. For the defects that have appeared, post-treatment technology is used to repair them. The application of these measures can significantly improve product quality and competitiveness.
1. Material selection: The right plastic material to ensure that the quality and characteristics meet the product needs is the first step to prevent surface problems.
2. Mold design: Optimizing the mold structure, such as reasonable gate and exhaust design, is the key link to reduce the defects of the plastic injection surface.
3. Injection molding process: Controlling the injection molding process parameters to ensure uniform melt flow and cooling is the guarantee for obtaining a high-quality surface.
4.Post-treatment: The use of appropriate post-treatment technology, such as grinding, spraying, etc., can effectively improve the surface quality of plastic injection products.
conclusion
Selecting the right material, optimizing the mold structure, precisely controlling the process parameters, and adopting the appropriate post-treatment technology can effectively prevent and solve various surface defects. It can not only improve the aesthetics and performance of products, but also extend their service life and enhance market competitiveness.
For expert assistance in implementing for your production needs, visit our resource center or contact us. Let’s help you scale up your manufacturing with precision and efficiency!
Post time: Mar-04-2025